The Audi has announced the start of production of the new generation of the A5 at the Neckarsulm factory in Germany, a facility where from 2025, all models produced will be carbon neutral.
To achieve this goal of the “360factory” production strategy, Audi is modernizing production lines and making them more efficient, with a higher degree of automation and innovative technologies. Next year, the factory will have a painting division that the company claims will be one of the most modern in the automotive industry.
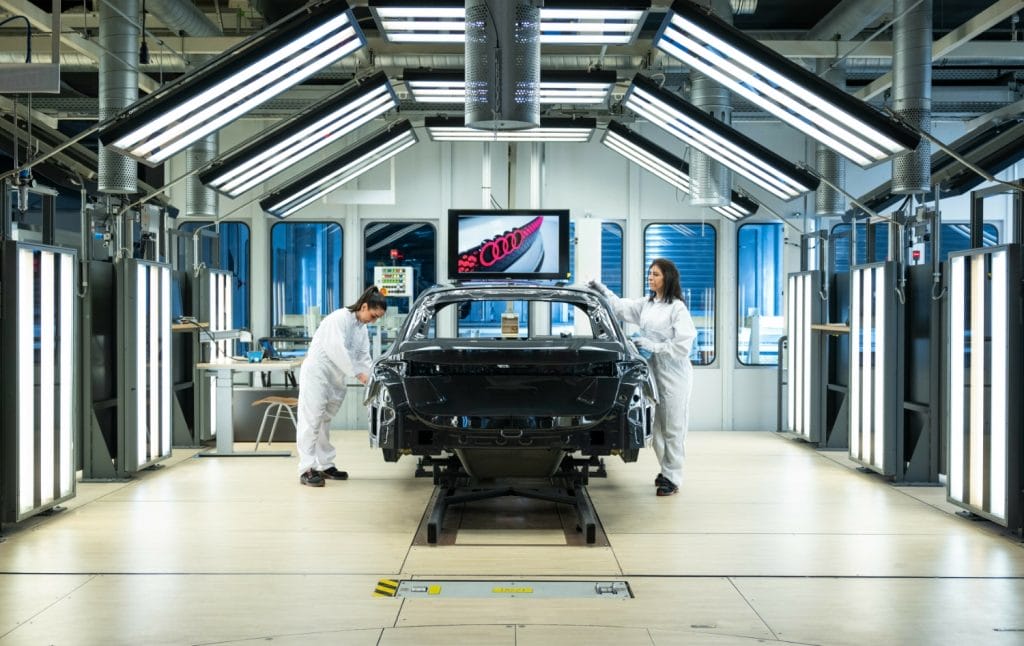
Various processes have already been optimized and ecological procedures have been introduced for the launch of the Audi A5. Although sustainable water-based paints have long been a standard at Audi, the latest models also undergo a new painting process. The primer is replaced by a paint that can be applied directly to the still wet base layer. The separate drying of the primer, previously required, is no longer necessary, allowing the four-ring brand to significantly reduce energy consumption: up to 140 kWh can be saved per vehicle.
In Neckarsulm, Audi uses modern and effective methods to prevent corrosion. Cathodic immersion painting, for example, involves immersing and rotating the body upside down in the tank through a rotation process. This method is more space-efficient and stricter, avoiding the formation of minimal air bubbles and dirt deposits. A new, more energy-efficient drying process is also used for cathodic immersion coating. Instead of the previous external drying process, a cross-flow drying process is now used. Air is blown inside, and the body is heated from the inside out. In addition to being more energy-efficient, the cross-flow dryer is more suitable for future electric and hybrid vehicles and their reinforced floor structures.
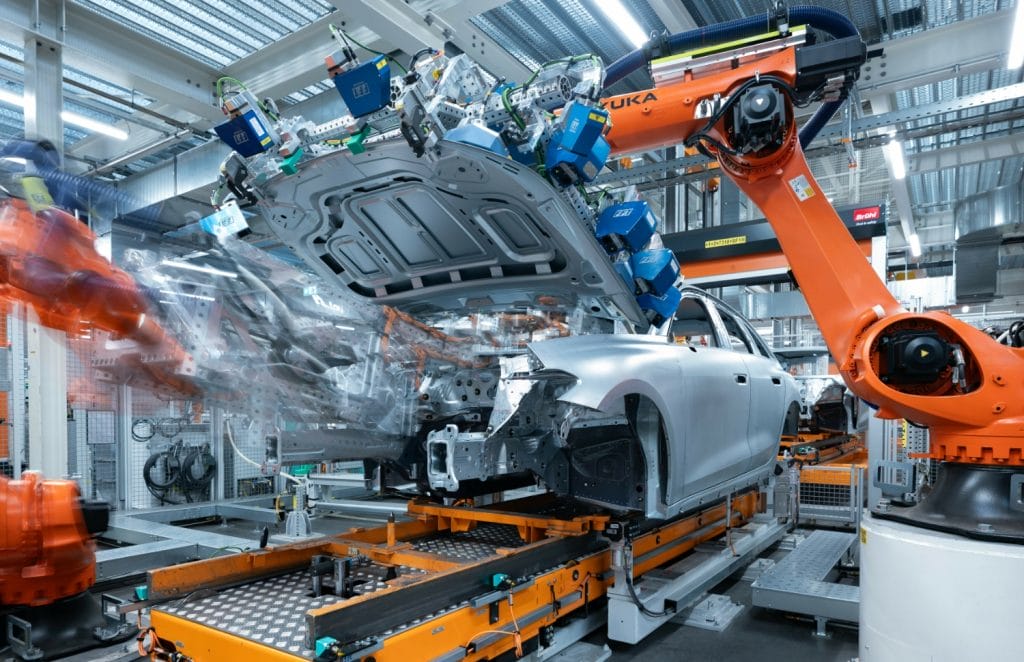
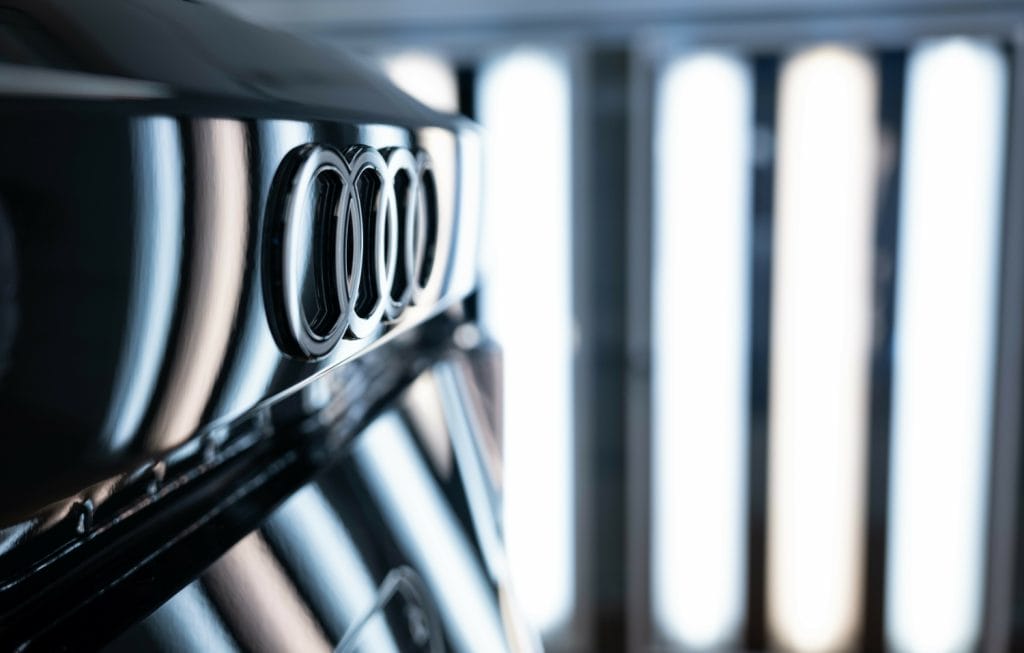
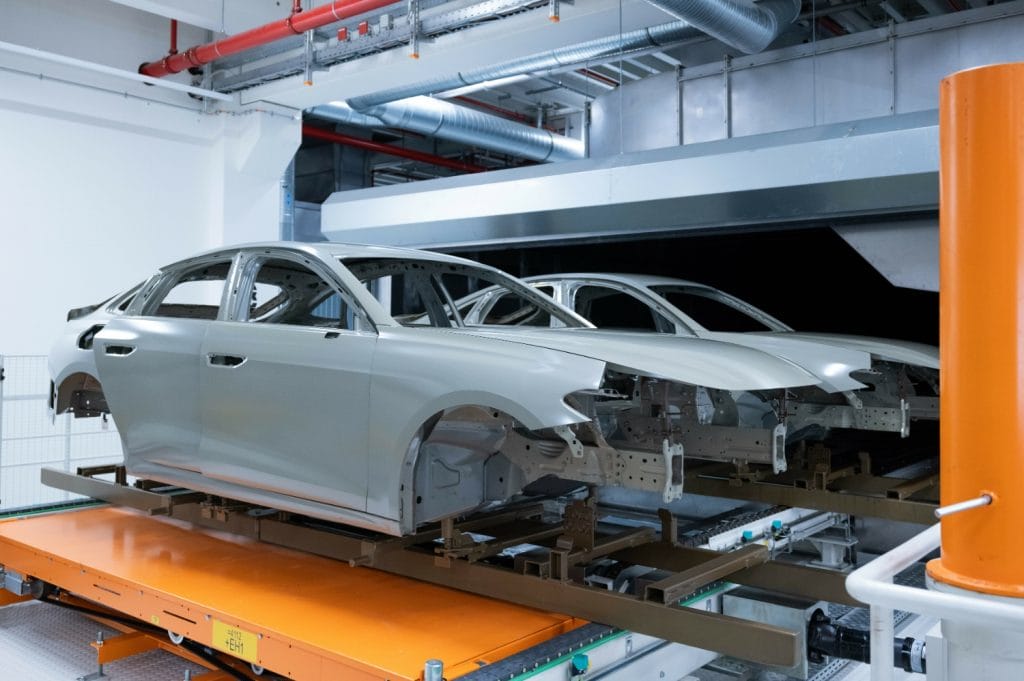
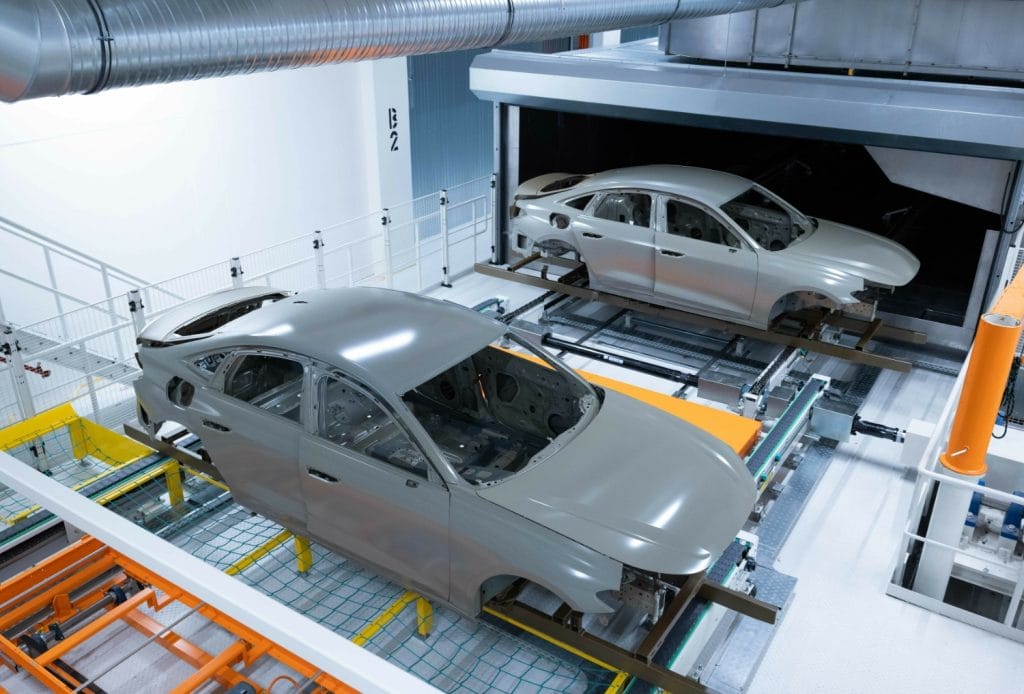
Audi achieves an additional energy savings of about 50 kWh per vehicle thanks to a new paint separation process. Previously, the paint mist was collected in water with 100% fresh air and discarded. In the new dry separation process, the paint mist is captured by state-of-the-art filters. This process allows more than 90 percent of the filtered air to be reused, largely eliminating the need for energy-intensive fresh air conditioning. At the same time, in contrast to conventional wet separation, the use of drinking water and chemicals is eliminated.
The four-ring brand is also making sustainable use of water at the Neckarsulm factory, with the aim of halving its ecologically weighted water consumption in production by 2035. To achieve this goal, the Audi production unit relies on a closed water cycle, using the wastewater treatment plant of the Unteres Sulmtal Wastewater Association, adjacent to the factory. New piping and treatment technologies ensure that no more process water will be taken from the nearby Neckar River canal. This will save up to 70% of drinking water from 2025. Audi will further treat the purified water from the wastewater treatment plant with the help of filter and membrane systems, allowing for economical and efficient water use.